Recently I stumble over a request for a fixed size of meter enclosures. Tolerances have also been given with +/- 2 mm, together with features like auxiliary circuits and exchangeable communication modules.
Basically this idea is not new. The German DIN 43857 family, issued in 1978 was already introducing a sort of standardization for several reasons. We take now only a look at the DIN 43857-1 (Singlephase meters up to 60 A)
- Housing depth max. 140 mm
this makes sure that all meters fit in the already existing cabinets and gives the cabinet designers clear information about new designs - Fixing holes for the meter, horizontal 105 mm (+/-1), vertical 155 mm (+/-1)
The meters can be exchanged without drilling new tapping. - Defined positions for the main terminals, dimensions are given from the vertical centre of the meter
This has many advantages. With standard terminals it is possible to do automated contacting for meter test and to equip the meter installations with fixed connection blocks for quick exchange of the meters. - Maximum size for overall dimensions
It's also helpful for planning and executing meter installations.
The DIN standard is old, but still valid. We have several clients asking for DIN compliant energy meters.
Around the year 2000 the first large smart meter rollouts started. A high degree of automation was necessary to make this meters cost effective.
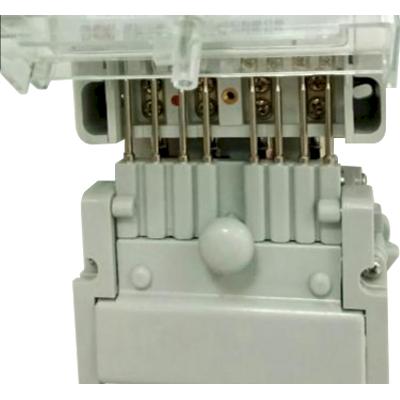
China has the world's largest smart meter installation with around 500 million end customers. The planning phase took about 5 years. Everything is defined in detail, including the meter colour. If you want to buy new moulds for a Chinese smart meter, the only questions is: "How many pieces?"
Not all countries or utilities have the resources or the need to make a complete planning like in China.
Some requirements for a meter housing definition
- Maximum outer dimensions of the housing and the terminal cover
- Position and size of the meter fixing holes
- Main Terminal size and position (x, y, z) from the vertical middle
- Position and size of the auxiliary terminals e.g.
– metrological pulse output, active energy
– metrological pulse output, reactive energy
– potential-free contacts
– interfaces (RS-485, RJ45) - Position of the LCD for automated display tests
- Position of the metrological diodes for automated accuracy tests
- Position of the IR communication port
- Position of push-buttons for automated function tests
Of course this needs also to do a proper planning. The box size must match with the requested features for communication modules and exchangeable battery. At the same time the utility need to make sure that the box and the power terminal sizes are large enough to avoid internal self heating.
Final thoughts
Standardization of energy meters can help to reduce cost. Giving only a meter box size without detailed planning is contra-productive. I don't know what other meter manufacturers are doing. We are not compromising in terms of safety.
I'm doing energy meter design and testing since more than 30 years and followed plenty of big projects. To make it simple, I still can't put my MacBook functionalities into a matchbox.
Are you a utility and planning a roll-out?
Are you a meter manufacturer and in need for production- and testing automation?
Talk to us, together we can find the optimized solution for your metering questions.
Thank you for reading.
Editor's note: This article was originally published in July 2020 and has been updated for comprehensiveness.
All comments are moderated before being published. Inappropriate or off-topic comments may not be approved.